衝撃試験の効率を最大化する緩衝可変機構
衝撃試験とは
様々な製品は、その使用中や流通過程のなかで、落下や衝突などで衝撃加速度が発生することで、製品が破損するトラブルに至ります。このような衝撃ハザードに対する品質管理や耐久性評価のために、製品開発段階で衝撃試験が実施されています。
ここでの衝撃試験とは、製品に衝撃加速度パルスを与える試験です。この試験の目的は、製品の耐久性確認、品質管理、損傷個所の特定などが挙げられます。また試験対象は完成品だけでなく、製品内部の各種部品にも適用されています。
衝撃試験は、振動試験機または衝撃試験機にて実施されます。要求される衝撃加速度パルスの最大加速度、速度変化が比較的小さい場合は振動試験機にて対応可能です。一方で、最大加速度が大きく、速度変化も大きい衝撃加速度パルスを要求される場合には、一般的に衝撃試験機(下図)が必要とななります。衝撃試験機の詳細な仕様はこちら
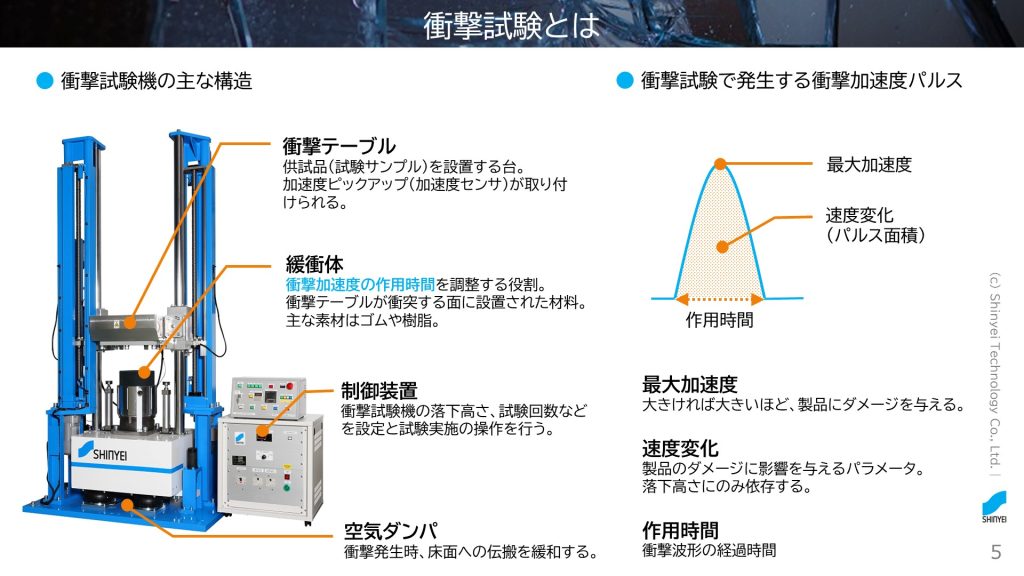
衝撃試験の効率化を実現する緩衝可変機構
衝撃試験で発生させる衝撃パルスの作用時間は、衝撃テーブルの衝突面に設置されている緩衝体(樹脂、ゴムなど)の硬度によって決まります。すなわち、緩衝体個別に発生できる作用時間は固定されることになります。ここで、衝撃パルスの作用時間を変更したい場合には、一般的な衝撃試験機の場合には、緩衝体そのものを取り換える必要がありますが、このとき試験現場では、以下のような課題が散見されます。
- 緩衝体交換は、人力で行うため、作業者の体力的負担が大きくなる
- 緩衝体交換には時間がかかるため、試験サイクルの効率が悪くなる(次の試験実施までに時間がかかる)
- 緩衝体は発生できる衝撃パルスの作用時間は決まっている。このため、当初予定していなかった新しい衝撃試験要求(作用時間の異なる)が出てきても対応はできない。
このような試験現場の課題を解決するために、緩衝可変機構(下図)が提案されています。この機構は、緩衝体の見かけ上の硬度(硬さ)を任意に変更することができる装置で、衝撃試験機ASQシリーズ、MDSTシリーズに搭載されています。
緩衝可変機能によるメリットは以下の通り。
- 緩衝体交換は緩衝リングの昇降のみのため、作業者の負担が大幅軽減
- すばやく試験条件を変更できることで、試験サイクルが向上
- 発生できる衝撃パルスの作用時間に幅※を持たせることができるため、新しい衝撃試験条件が追加されても対応可
※作用時間の範囲により対応できる条件は異なります。詳細は神栄テクノロジーまでお問い合わせください。
このように緩衝可変機構を搭載した衝撃試験機の活用により、衝撃試験の効率化が期待されます。より詳しい内容を知りたいかたは、↓より資料をダウンロードお願いします。